A finales de junio, Silvia y Sonia, las integrantes del equipo del Reto Lurbel que participarán en la RUN2 de la Dynafit Transalpine Run, viajaron a la sede de Lurbel, en Ontinyent, Valencia, para conocer a fondo cómo se fabrican las prendas, calcetines y el chaleco de hidratación de la marca valenciana que llevarán durante la prueba transalpina. De paso también tuvieron la oportunidad de conocer a sus compañeros de reto: la corredora del Lurbel Team Ana Tauste y su marido Javi Lurbe. Como pareja sentimental, para Ana y Javi será un reto si se compenetrarán corriendo en equipo igual de bien que lo hacen en la vida real; además han sido padres por primera vez hace unos meses, motivo por el que Ana empieza ahora a entrenar y coger ritmo para regresar a la competición después de dar a luz (su primera carrera ha sido en Val d’Aran).
Como siempre, los hermanos Lurbe y todo su equipo nos abrieron las puertas de su fábrica y de su casa y disfrutamos de una gran jornada: un entrenamiento matutino para conocer las montañas alrededor de Ontinyent y posteriormente la visita a su sede, donde Silvia y Sonia descubrieron todo lo que hay detrás de una prenda técnica de Lurbel y su proceso de fabricación, que pone especial énfasis en la producción sostenible: desde la elección de los materiales, pasando por la tejiduría y confección, hasta el resultado final con el producto ya empaquetado.
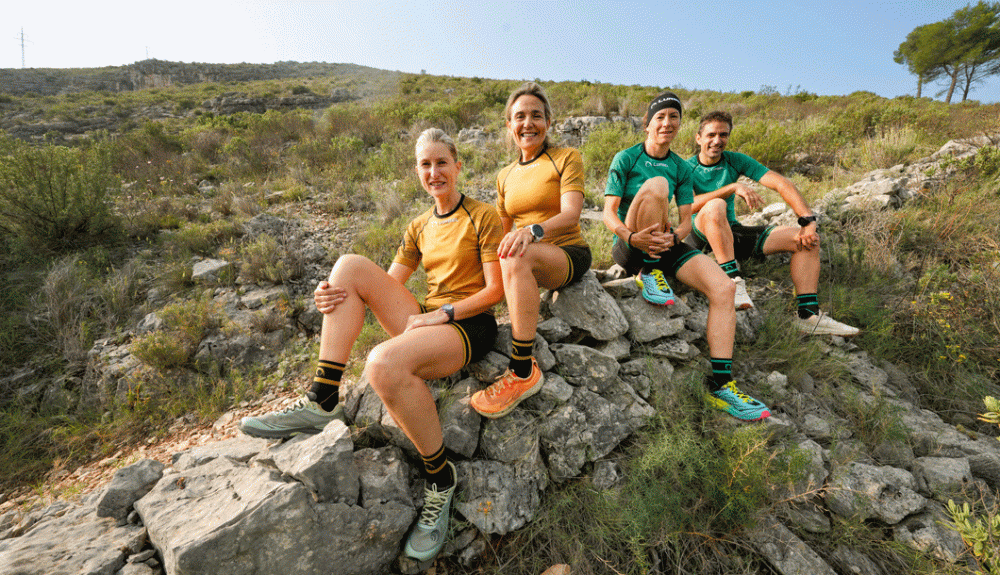
Y es que, como comentábamos durante nuestra visita a la fábrica y descubrir sus entrañas, parece un proceso sencillo, pero no lo es. ¿Os habéis parado alguna vez a pensar de qué está hecha esa primera capa que transpira y expulsa la humedad del cuerpo cuando estáis corriendo? ¿Sabíais que a lo mejor en un calcetín de trail running está fabricado con varios hilos diferentes, cada uno con unas cualidades distintas, repartidos en diferentes porcentajes para conseguir más transpiración, mayor amortiguación o refuerzos según las zonas? Yo no, desde luego no antes de entrar en la fábrica de Lurbel, y la verdad es que es sorprendente toda la investigación y análisis que hay en esos centímetros de hilo que apenas se ven.
Treinta años investigando en tecnología textil, mejorando el rendimiento de sus productos y pensando desde sus inicios en el futuro, apostando por esa difícil búsqueda del equilibrio entre producción y el respeto al medio ambiente. Lurbel se ha hecho un nombre más que destacado en el exigente sector textil deportivo internacional, y es que choca que una marca “made in Spain”, como proclaman con orgullo, sea un ejemplo a seguir en cuanto a producción de calidad y cada vez más sostenible. Una posición relevante que se han ganado los hermanos Lurbe a base de buen hacer, de una combinación entre conocimientos, experiencia y pasión por el sector textil y por el deporte. Ahora es difícil no encontrarse con alguien en el Camino de Santiago y que no lleve unos calcetines Lurbel con tecnología B Max, o participar en una carrera de montaña y que no lleve una camiseta o mallas realizadas con iDT Neo Recycled, pero hasta llegar aquí ha habido un largo camino…
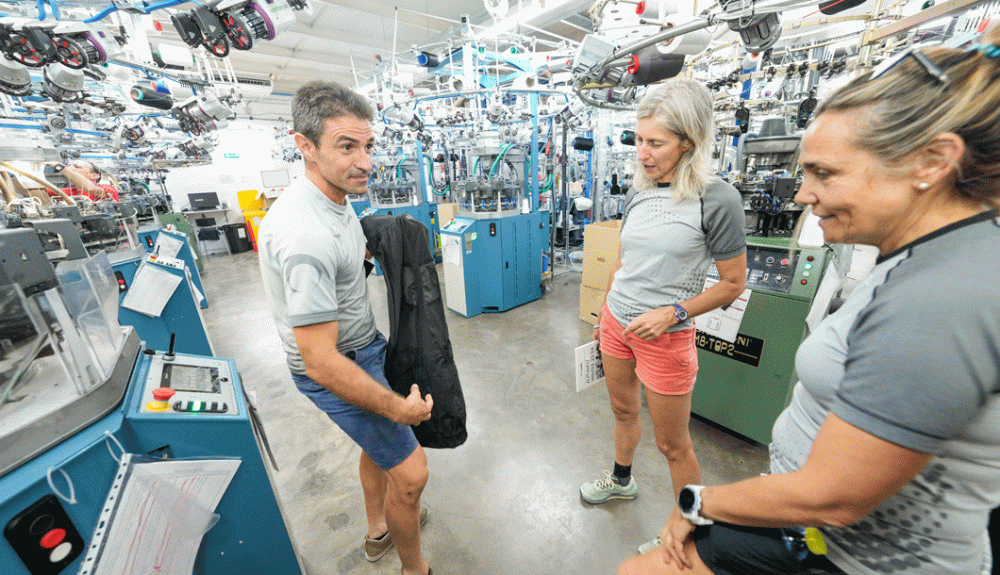
Silvia y Sonia pudieron conocer cómo se fabrican las prendas de Lurbel
Todo empezó hace cuatro décadas, en 1992, cuando Miguel Lurbe Sanz y sus dos hijos Miguel y Rafael fundaron una empresa centrada en la calcetería de punto en su localidad natal, Ontinyent, municipio valenciano de gran tradición textil. Antes ya estaban inmersos en el sector textil, concretamente en la producción de tejidos, pero decidieron cambiar a la calcetería impulsado por su espíritu emprendedor. Los tres hijos Miguel, Rafael y Javier crecieron con ese interés por el negocio familiar y entraron en la empresa consolidando el proyecto y posicionándose como un referente en este sector, pero la crisis de los años 2000 y una fuerte competencia les llevaron a adoptar un nuevo rumbo en expansión en ese momento: el sector deportivo (además que el deporte representa un ámbito muy importante de la vida de cada uno de ellos) especializándose en la fabricación no sólo de calcetines, sino también de otras prendas y complementos para practicar diferentes actividades deportivas al aire libre (trekking, mountain bike y ciclismo, trail running…) impulsando así la especialización del negocio familiar como garantía de éxito y diferenciación de la competencia. La idea pronto fraguó y nació la esencia de Lurbel tal como se conoce hoy en día.
Ahora es difícil no encontrarse con alguien en el Camino de Santiago y que no lleve unos calcetines Lurbel con tecnología B Max, o participar en una carrera de montaña y que no lleve una camiseta o mallas realizadas con iDT Neo Recycled, pero hasta llegar aquí ha habido un largo camino…
A partir de entonces esa especialización y diferenciación de otras marcas ha ido de la mano del I+D, de la búsqueda de nuevas materias primas y tecnologías, y de perfeccionar sus productos para mejorar a su vez la comodidad y el rendimiento de los deportistas. Y siempre con la mirada en el futuro, cuidando de esa naturaleza que tanto disfrutamos y apostando por la producción sostenible y la economía local. Paralelamente a la inversión en innovación, en Lurbel trabajan en la sostenibilidad, “uno de los ejes principales de las marcas que quieran liderar en este aspecto”, nos cuenta Rafa Lurbe, MS Textiles, fabricante y gerente de Lurbel. “Por ello, durante estos últimos años, hemos calculado la huella de carbono (HC) propia de nuestra actividad, tanto de la productiva como de la distribución de nuestras prendas desarrolladas en Ontinyent durante el periodo de 2017 a 2019. Durante esta etapa hemos adoptado algunas medidas con el objetivo de reducir nuestras emisiones de gases de efecto invernadero como, por ejemplo, la instalación de una planta fotovoltaica de autoconsumo en la cubierta de las instalaciones de nuestra sede así como la renovación integral de la maquinaria de la línea de planchado y tejeduría, esta última con sello “GREEN CERTIFIED” que garantiza un elevado rendimiento y una reducción drástica del consumo de energía". Otros de los pasos para reducir la huella de carbono que ha dado la empresa valenciana ha sido colaborar y trabajar con proveedores y materias primas de proximidad (en un radio de 30 km alrededor de Ontinyent). Y esta pasada primavera Lurbel lanzaba su primera colección monomaterial 100% reciclada.
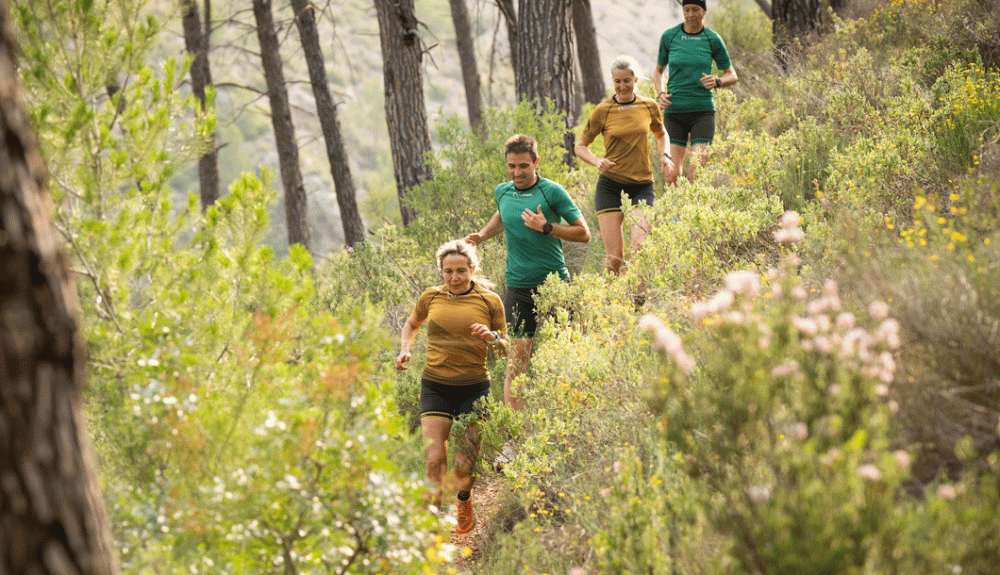
"Estamos en línea a todas las tendencias del mercado, tanto en producto como en sistemas de fabricación", nos comenta Rafa sobre esta colección y este proyecto Beta. "Consideramos que este inicio de proyecto va a marcar un poco la tendencia o el camino que Lurbel va a empezar a experimentar en todo el mundo de la sostenibilidad. Ya hemos dado pasos grandes internamente independientemente de esta colección, como por ejemplo en el consumo: a fecha de hoy estamos produciendo el 50% de la luz que consumimos, y la luz que no producimos, la contratamos de energías verdes, tenemos las máquinas de última generación con etiqueta de bajo consumo, con las que hemos reducido muchísimo el consumo de kilovatios. También hemos calculado la huella de carbono, y año tras año tenemos el reto de compensar esa huella. Llevamos dos años seguidos reduciendo ese cálculo inicial que teníamos. Son todos pequeños pasos que estamos dando para marcar un camino también en el mundo de la sostenibilidad, no sólo en el de la innovación y las prendas tecnológicas".
Después de visitar la fábrica, Silvia y Sonia pudieron probarse y recibir en mano la equipación que llevarán durante esas dos exigentes etapas de la RUN2: camiseta y mallas Spirit, los calcetines Desafío Spirit Four, manguitos, un chaleco Kylie Pro y un cinturón Loop Pro. Javi Lurbe les explicó todas las propiedades de las prendas y chaleco que van a llevar, esas prendas que ahora conocen mucho mejor, y que han podido ver cómo se fabrican desde el punto cero a su venta final.
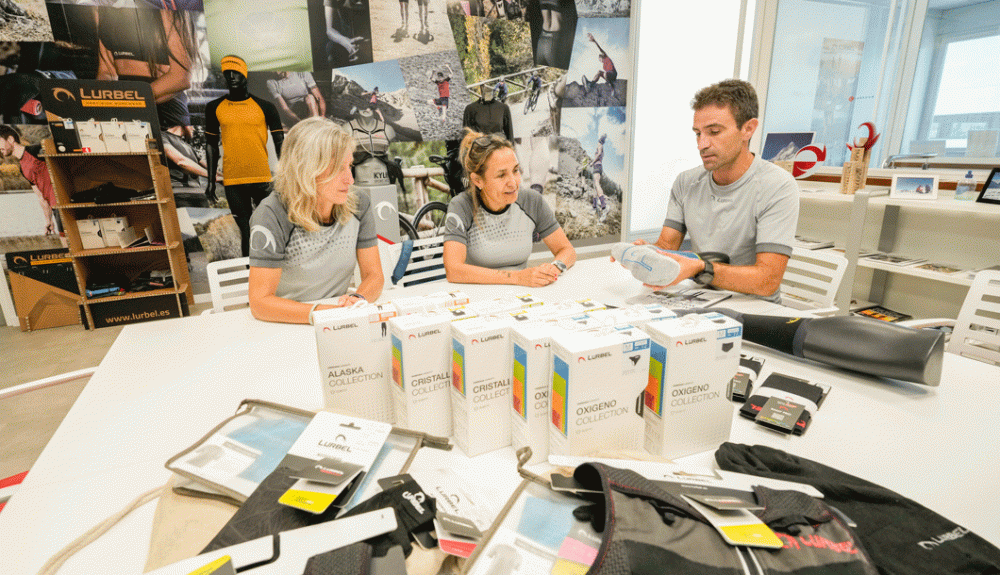
Después de este interesante y enriquecedor encuentro, sólo queda seguir entrenando duro y probar las prendas hasta que llegue la hora de afrontar el Reto Lurbel TAR, elpróximo 8 de septimbre. ¡Vamos equipo!
www.lurbel.eu